Plastics
Plastics
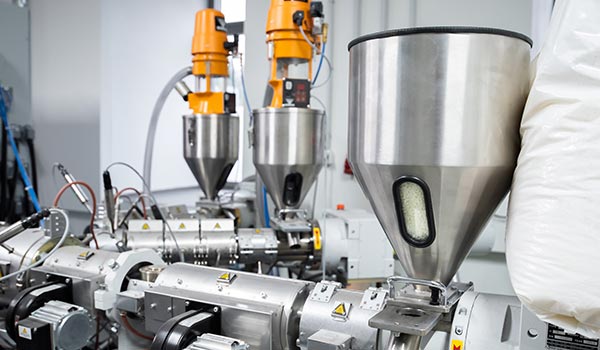
The methods of improving plastic glossiness include two aspects: one is to improve the surface
glossiness of plastic products, which is called brightening modification, and the other is to
reduce the surface glossiness of plastic products, which is called extinction modification. The
following are the main ways to enhance brightness of plastics:
The brightening of plastics is to improve the surface gloss or finish of plastic products. Except
from reasonable selection of raw materials, the specific brightening methods include adding
additives, morphological controlling, plastic blending, controlling the finishing degree of
molding equipment, secondary processing and surface coating and so on.
Selection of plastic raw materials
The reasonable selection of plastic raw materials is the most basic factor to improve the
surface glossiness of plastic products. If the raw material is selected well, it is easy to improve
the glossiness; otherwise, it is more difficult.
Plastic raw materials can be divided into two major categories: a)resin and additives,
b)Selection of resin. The characteristics of resin have great influence on the surface gloss of
plastic products, which is the most effective method to control the surface gloss of plastic
products. Its impact on the surface gloss of plastic products mainly depends on the following
aspects:
1) Varieties of resins
The gloss of the corresponding products varies greatly with the variety of resins. It is generally
considered that the gloss of the following corresponding products is better: melamine
resin>ABS>PP>HIPS>PA>POM>PMMA>PPO, among which melamine resin and ABS have the
most outstanding gloss.For the same resin, the gloss of the corresponding product is different
with different synthetic methods. For example:
A)For PP, the gloss degree of different polymerization methods is as follows: PP-R>
homopolymerization PP> block copolymerization PP.
B) For PE, the gloss of three different varieties is as follows: LDPE > LLDPE > HDPE
C) For PVC, the gloss of emulsion PVC resin is higher than suspension PVC resin.
D)For PS resin, the gloss of high impact HIPS is higher than that of GPPS.
2) Properties of resin
For the same resin, with different properties, its glossiness is different. Among the properties
of the resin, the following are the main ones that affect the glossiness of plastic:
a) The larger the melt flow rate (MFR) is, the greater the gloss of the product is.
b) The influence of molecular weight: The influence of molecular weight is mainly reflected in
the width of molecular weight distribution. Wider the molecular weight distribution, the lower
the gloss of the product. This is mainly due to the wide distribution of molecular weight causing
the increase of the irregularity of materials.
c) The effect of water absorption. The resin with high water absorption rate has a great
influence on the gloss of the corresponding products. For example, (-COOR) and (-CONH2) in
the molecule, if they are not dried or not dried thoroughly, water ripples, bubbles, silver wire,
stripes, wool defects and so on will be produced on the surface of the product, so that the
surface gloss will be greatly reduced.
Gloss of plastics
3) Selection of additives
Of all the additives for plastics, fillers have the greatest effect on glossiness, and plasticizers,
stabilizers and flame retardants have less influence.
Effect of fillers: The effects of fillers on gloss can be divided into the following aspects:
The effects of different filler varieties on gloss are different. Almost all fillers except glass
beads will reduce the gloss of the fillers, but by different degrees.
The order of influence of several fillers on the gloss of filling products is as follows: metal salt
> glass fiber < talc powder < mica
The influence of the glossiness of depends from shape of filler products varies according to
the microcosmic shape of filler particles. And the order of influence is as follows: globular <
granular < needle-shaped < flake.
Particle size of fillers
The smaller the size of the filler is, the lower the gloss of the filler is. In addition, the dispersion
of distribution of the filler is different, and the effect on the gloss of the filled products is
different. The influence law is: the wider the distribution of the filler, the lower the gloss of
the filler surface. This is mainly because the bigger the difference of the size of the filler is, the
surface is more convex and uneven, and the incident light is more likely to generate diffuse
reflection.
Filler of amount
The surface gloss of the filler product decreases with the increase of filler. Taking CaCO3 filled
PP system as an example, when CaCO3 filling is 5%, the surface gloss of the filled product is
50%. When the CaCO3 fill is 15%, the gloss of the filling product drops to 32%.
PVC Processing Additives Selection Principle
PVC processing auxiliaries are a kind of auxiliaries which can improve the processing
properties of resins. The ductility of POLYvinyl chloride melt is poor, which leads to melt
breakage easily. Polyvinyl chloride melt relaxation is slow, easy to lead to rough surface, matt
and "shark skin". Therefore, polyvinyl chloride processing often need to add processing AIDS
to improve its melt defects.
The use of notes:
Polyvinyl chloride mixtures are usually processed with a variety of processing AIDS. Different
types of processing AIDS can be used together to achieve better processing performance.
Mainly can be used in the production of blow molded containers, calendring or extrusion
sheet, wall panels, profile extrusion, high flow injection molding parts, pipe fittings, pipe
wrapping and many other aspects. The balance between rheological properties of melt,
homogeneity of melt and thermal demoulding properties of metal not only affects the
appearance quality, but also affects the production efficiency. Whether the dosage of each
component is appropriate is very important, it will affect the quality of the product,
transportation and storage must be moisture-proof, sun protection and anti-fouling.
PVC processing AIDS to promote plasticizing, lubricity. Widely used in, PVC doors and
Windows, pipes, pipe fittings, decorative board, foam board, sheet, film, wood plastic
transparent plastic and other hard products processing
Calcium zinc
Calcium zinc stabilizers are a non-toxic heat stabilizers synthesized by special composite
process with calcium salt, zinc salt, lubricants and antioxidants as the main components. It is
one of the important additives for heat sensitive polymeric materials, such as PVC, PVDC,
PCTFE, CPVC, neoprene, etc., to prevent or delay its thermal degradation.
Action mechanism of calcium zinc stabilizer
1. It can replace the active groups in the polymer chain (such as the chlorine atom in the allylic
position in PVC) to obtain a more stable polymer, so as to eliminate the initiator of
dehydrochlorination in the polymeric materials and reduce the possibility of initiating
dehydrochlorination reaction.
2. It can quickly capture the fallen hydrogen chloride and inhibit its autocatalysis.So what the
role of polyethylene wax in calcium zinc stabilizer? In the processing and manufacturing of
various soft and hard PVC products, not only heat stabilizers but also lubricants are needed.
Calcium has poor lubricity, so wax additives need to be added to improve the lubrication effect
of the product.
WAXES
The performance improvement of oxidized polyethylene wax on a calcium zinc stabilizer is as
follows:
1. Oxidized polyethylene wax contains hydroxyl and other functional groups, which can
improve the thermal stability of Ca / Zn stabilizer.
2. Improve compatibility with PVC, reduce frost spraying, and improve printability and heat
sealing.
3. Promote plasticization and improve the fluidity for PVC material.
4. The excellent lubrication effect endows calendering, extrusion, injection and blow
molding equipment with good metal demoulding.
Waxes based in Fischer Tropsch method
Fischer Tropsch wax is a methylene polymer, which is an alkane synthesized from
hydrocarbon based synthetic gas or natural gas. It is composed of 90 ~ 95% of conventional
paraffin hydrocarbons, and the rest are tertiary hydrocarbons and methyl hydrocarbons with
branches at the molecular end. Fischer Tropsch (FT) synthesis refers to a production process
of synthesizing alkanes from carbon monoxide and hydrogen under high pressure with a
unique catalyst. According to the requirements of downstream products (such as fuel,
lubricating oil and wax), FT process can synthesize alkanes with different chain lengths and
separate alkanes by distillation. Carbon monoxide and hydrogen are synthesized,
fractionated, solvent extracted and bleached under certain pressure, temperature and
catalyst conditions. According to the needs, the molecular weight of the final product can be
changed, so that the high melting point wax can be obtained from the monomer hydrocarbon
similar to liquid paraffin to the high melting point wax similar to polyethylene wax, which has
the special properties that other natural waxes or other synthetic waxes do not have. It has
better electrical properties than paraffin, higher melting point and hardness, and narrower
fraction. According to the needs, the molecular weight of the final product can be changed,
so that the high melting point wax can be obtained from the monomer hydrocarbon similar
to liquid paraffin to the high melting point wax similar to polyethylene wax, which has the
special properties that other natural waxes or other synthetic waxes do not have. It can
replace carnauba wax in luster. The internal and external lubricants of various plastics are
used to produce Duroc pine wax and develop a wider range of applications.
Fischer Tropsch wax belongs to high molecular inert material, which has the characteristics
of low viscosity, high softening point, high melting point and excellent lubrication performance.
It is widely used in industrial production. Suitable for concentrated masterbatch,
polypropylene masterbatch, additive masterbatch, filling masterbatch and other pigments or
filler dispersant, lubricant, brightener, coupling agent. Rubber and plastic processing
lubricant, remover and solvent, OPE wax, all kinds of rubber and good intermiscibility, due to
its high melting point and low viscosity, good prompted the resin flow, relative to reduce resin
hybrid power consumption, to reduce the mold and the resin adhesion, easy to take off the
membrane, internal and external lubrication role, at the same time has good antistatic
property. As a water-based coating and ink anti - adhesion additives and anti - friction
additives. As a viscosity regulator of thermal sol.
F-T wax can be use for shoe polish, floor wax, wax polish, car wax, cosmetics, matches wax
rod, wear-resisting agent of printing ink, ceramics, precision casting, oil absorbent, sealing
daub, hot melt adhesives, cable feed additive, oil well paraffin remover, crayon, carbon paper,
waxed paper, inkpad, photographic materials, textile softener, matrix electronics sealant,
transistor packet agent, rubber processing aid , automobile bottom oil, dental material
processing AIDS, steel rust inhibitor, etc.
Uses: Widely used in water-based coatings and ink formulations to provide excellent abrasion
resistance, adhesion resistance and scratch resistance.
In the plastic processing industry, the internal and external lubrication of PVC is more
balanced; In the hard transparent, opaque PVC formula adding oxidized polyethylene wax its
lubricity is better than other lubricants. It is widely used in PE, PVC cable production, PVC
profile, pipe production, can be regarded as an excellent new plastic processing lubricant. Can
also be used for textile softener, car wax, leather softener production raw and auxiliary
materials.
Chlorinated Polyethylene (CPE)
CPE has the dual properties of plastic and rubber, and has good compatibility with other
plastics and rubber, so most of CPE is used with rubber or plastic except for a few main
materials. CPE is mainly used as a modifier when used with plastics. Its main use is as an antiimpact
modifier for hard polyvinyl chloride (UPVC) products, and improve the impact
resistance and low temperature performance of UPVC. It can be used to manufacture UPVC
Windows and doors profiles, pipes and injection products. When used with rubber, CPE mainly
improves the flame retardant, insulation and aging resistance of rubber. In addition, can be
used as flame retardant ABS resin modifier, can also be used as injection PVC, PC, PE impact
modifier. Chlorinated polyethylene (CPE) is a powdery product of suspended chlorination of
HDPE in aqueous phase. With the increase of chlorination degree, the original crystallized
HDPE gradually becomes an amorphous elastomer. CPE used as toughening agent usually
contains 25-45% C1. CPE sources widely, low price, in addition to toughening effect, but also
has cold resistance, weather resistance, fire resistance and chemical resistance.
Chlorinated polyethylene (CPE) is a saturated polymer material with the appearance of white
powder, non-toxic and tasteless. It has excellent weather resistance, ozone resistance,
chemical resistance and aging resistance, and has good oil resistance, flame retardant and
coloring performance. Good toughness (still flexible at -30℃), good compatibility with other
polymer materials, high decomposition temperature, decomposition of HCl, HCl can catalyze
the dechlorination reaction of CPE.
Chlorinated polyethylene is a kind of high density polyethylene (HDPE) by chlorination
substitution reaction. According to different structure and use, chlorinated polyethylene can
be divided into resin type chlorinated polyethylene (CPE) and elastic type chlorinated
polyethylene (CM) two categories. Thermoplastic resin can be used alone, but also with
polyvinyl chloride (PVC), polyethylene (PE), polypropylene (PP), polystyrene (PS), ABS and
other resins and even polyurethane (PU) blends. In the rubber industry, CPE can be used as a
high-performance, high-quality special rubber, but also can be used with ethylene-propylene
rubber (EPR), butyl rubber (IIR), nitrile rubber (NBR), chlorosulfonated polyethylene (CSM) and
other rubber blends.
PROCESSING AIDS
As an ideal rigid PVC processing aid, ACR impact modifier has been widely recognized, and can
be added to any rigid PVC products according to different processing needs. Polyvinyl chloride
mixtures are usually processed with a variety of processing AIDS. Different types of processing
AIDS can be used together to achieve better processing performance. Mainly can be used in
the production of blow molded containers, calendring or extrusion sheet, wall panels, profile
extrusion, high flow injection molding parts, pipe fittings, pipe wrapping and many other
aspects. The balance between rheological properties of melt, homogeneity of melt and
thermal demoulding properties of metal not only affects the appearance quality, but also
affects the production efficiency. Whether the dosage of each component is appropriate is
very important, it will affect the quality of the product, transportation and storage must be
moisture-proof, sun protection and anti-fouling.
PVC processing AIDS to promote plasticizing, lubricity. Widely used in, PVC doors and
Windows, pipes, pipe fittings, decorative board, foam board, sheet, film, wood plastic
transparent plastic and other hard products processing.
Application: The average molecular weight of the modified ACR is much higher than that of
the common PVC resin. Its main function is to promote the melting of PVC resin, change the
rheological properties of the melt and improve the surface quality of products. Application
scope: 1: profile 2: pipe 3: pipe fittings 4: plate 5: gusset plate, etc.
In the production of PVC products, ACR impact modifier can effectively improve the processing
properties of PVC profile formula, promote the plasticization of PVC particles, reduce
the processing temperature and melt viscosity, improve the plasticization properties of PVC
and also ensure good processing fluidity. At the same time, due to its good compatibility with
PVC. It can be more advantageous to adapt to the production of low cost, good physical and
mechanical properties of PVC products. At present, it has been widely used in the production
of PVC profiles, pipes, pipe fittings, plates and wood-plastic products.
Advantages of ACR Impact Modifier Products:
1. The special bimodal molecular structure can rapidly promote the plasticization of PVC in
the process of processing and still maintain good processing fluidity;
2. Special production process, the product particle size is far less than the traditional ACR
additives, in the PVC products in the dry mixture dispersion probability is greater, the
distribution is more uniform, so that the production and product performance is more stable;
3. With special production technology and raw materials, the unit cost of the product is more
than 20% lower than that of traditional ACR additives, which greatly saves the production cost
for customers;
4. Excellent formula design gives excellent comprehensive performance to the production of
PVC products, and comprehensively improves the appearance finish, tensile impact
performance and welding Angle strength of customers' PVC products.
ACR is a copolymer of methyl methacrylate, acrylate and other monomers. ACR is the best
impact modifier developed in recent years. It can increase the impact strength of materials by
dozens of times. ACR is an PVC impact modifier with core-shell structure. It is a shell composed
of methyl methacrylate and ethyl acrylate polymer. The chain segments of butyl acrylate
crosslinked rubber elastomer are distributed in the inner layer of particles. It is especially
suitable for the impact modification of PVC plastic products used outdoors.
With the deepening of the company's understanding of PVC plasticization mechanism, PVC
processing technology and PVC equipment, we have developed a series of processing aids for
the defects of processing equipment and the performance defects of PVC products. These
processing aids are different from traditional processing aids, which break through the
limitation of traditional processing aids and solve a series of practical problems that traditional
processing aids cannot solve. Specifically, PVC processing aids are making major
breakthroughs in the following directions.
(1) Super plasticizing processing assistant
It is suitable for the high filling volume, large external sliding dose and weak shear force of
equipment. It needs to greatly improve the shear force, strengthen plasticization and improve
the viscosity of melt strength. It can make up for the decrease of melt viscosity caused by the
weak shear force of equipment and the large filling volume in the formula. It breaks through
the traditional processing aids with low melt viscosity and low plasticizing speed when the
melt viscosity is high There are many defects in it.
(2) Super melt strength processing assistant
It is suitable for the use of high filling volume and strong shear force of equipment, so it needs
to be used when the melt strength is greatly improved. The characteristics of these processing
aids are that the plasticizing speed is general, but the melt viscosity is large, which is more
than 3 times of the traditional processing aids ACR.
MBS
MBS is a copolymer of methyl methacrylate, butadiene and styrene. The solubility parameter
of MBS is between 94 and 9.5, which is close to that of PVC, so it has good compatibility with
PVC. Its biggest feature is that it can be made into transparent products after PVC is added.
Generally, adding 10-17 copies of people to PVC can increase the impact strength of PVC by
6-15 times, but when the amount of MBS is greater than 30 copies, the impact strength of
PVC decreases instead. MBS itself has good impact performance, good transparency, light
transmittance can reach more than 90%, and improve the impact at the same time, on the
other properties of resin, such as tensile strength, elongation at break and so on little impact.
MBS has a high price and is often used with other impact modifiers, such as EAV, CPE and SBS.
MBS heat resistance is not good, poor weather resistance, not suitable for outdoor long-term
use of products, generally do not do plastic doors and Windows profile production impact
modifier use.
Impact Modifiers
PVC impact modifiers sometimes also play a plasticizing role at the same time, so can also be
seen as plasticizers. Promoting PVC fusion and modifying melt rheology.Sometimes have role
for improvement of PVC processability which is a key factor in determining the appearance
and physical properties of the PVC. PVC resin is a polar non-crystalline polymer, there is a
strong force between the molecules, is a hard and brittle material, the impact strength is low.
After adding the impact modifier, the elastomeric particles of the impact modifier can reduce
the total silver grain initiating stress and use the particles' own deformation and shear band
to prevent the silver grain from expanding and growing, absorbing the impact energy
transmitted into the body of the material, thus achieving the purpose of impact resistance.
Modifier particles are small to facilitate the increase in the number of modifiers per unit
weight or unit volume, so that their effective volume share increases, thereby enhancing the
ability to disperse stress.
Plasticizers
Phthalates, the most commonly used plasticizers in PVC, are known endocrine disruptors –
chemicals that interfere with hormone signaling, which is especially critical to early childhood
development.In response to consumer and regulatory pressures, PVC building products
manufacturers have begun to offer phthalate-free products. Even without phthalate
plasticizers, the lifecycle of PVC has inherent toxicities that cannot be avoided. At its core, PVC
relies upon chlorine chemistry that forms toxic byproducts from its manufacture to its
disposal. While the elimination of phthalate plasticizers from PVC does not these solve
inherent problems, it does provide a specific relief to building occupants who are otherwise
exposed through the everyday use of PVC products.
Mainly more friendly plasticizers are:
• Diisononyl cyclohexane-1,2-dicarboxylate (DINCH)
• Di-(2-ethylhexyl) terephthalate (DEHT a.k.a DOTP)
• Dibenzoates [commonly Dipropylene glycol dibenzoate (DGD) or a blend
• of DGD, Diethylene glycol dibenzoate (DEGD), and Triethylene glycol
• dibenzoate (TGD)]
• Acetylated monoglycerides of fully hydrogenated castor oil (COMGHA)
• Ecolibrium [of vegetable oil based blend]
• Isosorbide diesters
Overall, COMGHA and Isosorbide Esters appear to be the best with few data gaps and low
toxicity during manufacture and in use. While the replacement of toxic phthalate plasticizers
is a necessary step for PVC, this should not distract from the intractable environmental health
issues that plague the PVC lifecycle and still necessitate its avoidance in the built environment.
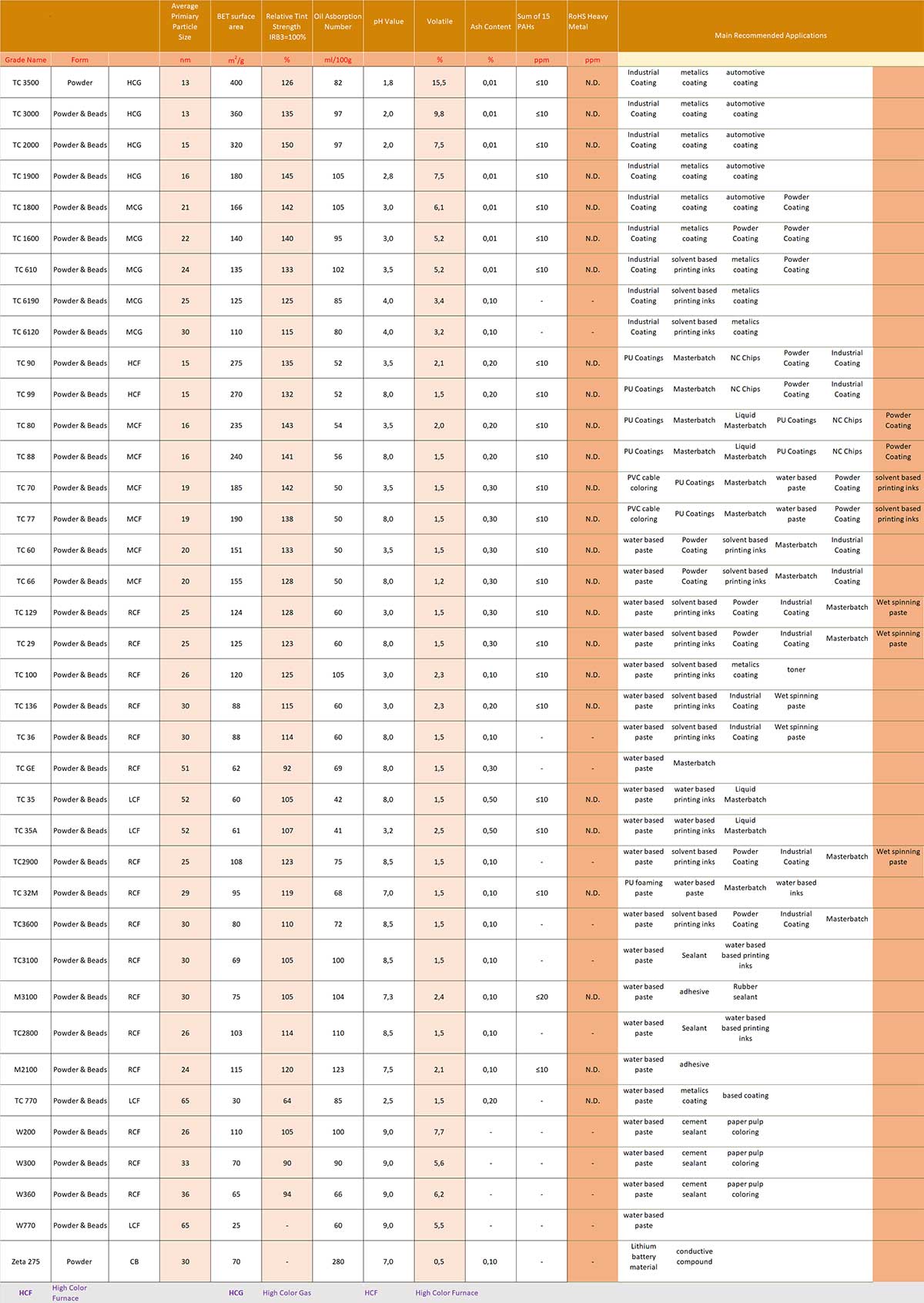
GET IN TOUCH
Send Us a Message and Learn More About Our Services and Products
Our representative will contact you as soon as possible.